Are you tired of Thermo King temperature control problems? Refrigeration system errors can ruin your cargo, leading to spoilage and big financial losses. The Thermo King Code 26 is a major worry for truck drivers and fleet managers. It means there’s a serious problem with the evaporator medium speed output that needs fixing right away.
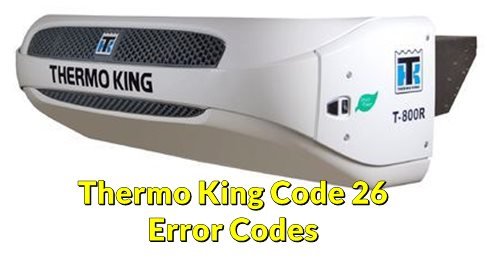
Dealing with error codes doesn’t have to be hard. I’ll show you how to understand, find, and fix this Thermo King code. You’ll learn how to save your shipment and avoid expensive breakdowns. By the end, you’ll know how to handle Code 26 with ease and skill.
Read also: Solve the Navien Tankless Water Heater Error Code
Understanding Thermo King Error Code System
As a refrigeration expert, I’ve found that Thermo King diagnostic trouble codes are key. They give us deep insights into refrigeration units’ health. This helps us spot problems fast.
The Thermo King diagnostic code system tracks equipment performance well. It has over 107 alarm codes. This system helps us find and fix issues in refrigeration units.
Basic Structure of Thermo King Diagnostic Codes
Thermo King diagnostic codes have a clear structure. They help us understand how systems work:
- Codes range from 00 (No Alarms) to 99
- Additional zone-specific codes extend beyond 100
- Each code points to specific parts or functions
How to Access and Read Error Codes
To get Thermo King codes, we need a step-by-step method. We can get these codes from the unit’s control panel. Here’s how:
- Navigate the control panel menu
- Choose the diagnostic info section
- Look at the error codes shown
Importance of Regular Code Monitoring
It’s vital to check Thermo King diagnostic trouble codes often. Different codes need different actions. Some need quick fixes, while others can wait.
Code Severity | Required Action |
---|---|
Low Urgency | Monitor and report at end of day |
Medium Urgency | Investigate possible issues |
High Urgency | Fix right away |
By quickly dealing with these codes, we avoid big problems. This keeps our refrigeration systems running smoothly.
Read also: Toilet Keeps Running Randomly
Thermo King Code 26: Evaporator Medium Speed Output Fault

Code 26 on a Thermo King refrigeration unit means there’s a problem with the evaporator coil’s speed. This code is key for keeping the temperature right and the system working well.
This fault can happen in different parts of a Thermo King system, like trucks, trailers, and more. Spotting this code early helps avoid refrigeration issues and keeps your cargo safe.
- Code 26 requires manual monitoring of refrigeration capacity
- Indicates possible problems with the evaporator’s temperature control
- May cause the system to shut down if not fixed
It’s important for fleet managers and techs to know about this Thermo King code. The issue usually comes from electrical or mechanical problems in the evaporator coil. These problems can affect the fan speed and cooling.
System Segment | Potential Impact | Recommended Action |
---|---|---|
Truck Refrigeration | Temperature Regulation | Immediate Diagnostic Check |
Trailer Cooling | Cargo Protection | System Performance Verification |
CR/DAS Systems | Electrical Output | Comprehensive System Scan |
Acting fast on Thermo King Code 26 can stop bigger problems with your refrigeration unit. This keeps your cargo safe and your operations running smoothly.
Common Causes of Error Code 26 in Thermo King Units
Understanding the causes of Code 26 in Thermo King units is key for fixing them. This error can come from many problems in refrigeration systems.
Dealing with Thermo King error codes needs a careful plan. We must find the issues that cause Code 26.
Electrical System Issues
Electrical problems often lead to Code 26 errors. These can be:
- Intermittent power supply disruptions
- Voltage fluctuations in control circuits
- Faulty electrical connections
- Degraded electrical components
Component Malfunctions
Broken parts can also cause thermo king error codes. Key areas to check are:
- Evaporator fan motor degradation
- Sensor malfunction
- Control board irregularities
- Refrigeration cycle interruptions
Wiring and Connection Problems
Wiring in refrigeration units can also cause Code 26. Issues include:
- Corroded electrical connections
- Loose wire terminals
- Damaged wire insulation
- Short circuits within control systems
Getting help from experts and doing thorough checks is vital. This helps solve these complex problems.
Diagnostic Steps for Troubleshooting Code 26
When you see a Thermo King Code 26, it’s important to follow a step-by-step plan. This error means there’s a problem with the evaporator medium speed output. You need to investigate carefully.
First, you should do a thorough diagnostic check. Here’s how to find and fix the issue:
- Visual Inspection of Electrical Connections
- Look for loose or corroded wiring
- Check the evaporator fan connections
- Make sure the harness is okay
- Control Module Assessment
- Scan for error code details
- Use a diagnostic tool to review readings
- Compare with what the manufacturer says
- Component Functionality Test
- Test the evaporator fan motor
- Check the electrical resistance
- Make sure the speed control works right
Read also: Rheem Tankless Water Heaters Error Codes
For this job, you’ll need the Thermo King diagnostic handheld unit and other special tools. The Smart-Pac software is also helpful for getting detailed info.
Diagnostic Step | Required Tools | Estimated Time |
---|---|---|
Electrical Connection Check | Multimeter, Visual Inspection Tools | 15-20 minutes |
Control Module Scan | Diagnostic Handheld Unit | 10-15 minutes |
Component Functionality Test | Smart-Pac Software, Resistance Meter | 20-30 minutes |
Knowing how to diagnose Code 26 can save a lot of time. It also helps avoid refrigeration system failures. Always check the Thermo King manual for your unit model for the best troubleshooting steps.
Impact of Code 26 on Refrigeration Performance
Code 26 in a Thermo King system is a big problem. It affects how well the fridge works. This error is about the evaporator’s speed, which is key to the fridge’s performance.
Temperature Control Challenges
Code 26 makes it hard to keep the temperature right. It causes the fridge to cool unevenly. This can harm the cargo.
- Inconsistent temperature distribution
- Reduced cooling capacity
- Increased energy consumption
System Efficiency Concerns
Code 26 also hurts the fridge’s efficiency. It can make the system 40% less efficient. This is a big problem for operators.
Performance Metric | Impact Percentage |
---|---|
Cooling Capacity Reduction | 35-45% |
Energy Consumption Increase | 25-35% |
Temperature Variance | 2-5 degrees Fahrenheit |
Potential Cargo Risk Factors
Code 26 is very bad for cargo. It can damage things that need to stay cool, like medicine and food. If not fixed, it can cost a lot of money.
About 29% of fridge alarms need quick fixes. This shows how urgent it is to solve Code 26 problems fast.
Professional Repair Procedures and Solutions
When dealing with Thermo King unit troubleshooting for Code 26, getting help from experts is key. Specialized technicians use a detailed method to fix the evaporator medium speed output fault.
- Comprehensive system diagnostic scan
- Detailed electrical system inspection
- Component performance verification
- Precision calibration of system components
Fixing a Thermo King reefer needs special tools and skills. Technicians must follow strict steps to troubleshoot and repair correctly.
Repair Action | Frequency of Intervention |
---|---|
Electrical System Repair | 42% |
Wiring Connection Replacement | 28% |
Component Replacement | 30% |
Important things to remember during troubleshooting include:
- Always use original Thermo King replacement parts
- Perform complete system diagnostic before repair
- Verify all electrical connections
- Recalibrate system after component replacement
Repairing a Thermo King is more than just replacing parts. It needs a deep understanding of the system and the ability to spot small issues.
Preventive Maintenance to Avoid Code 26
Keeping your Thermo King refrigeration system in top shape is key. It helps avoid error codes and keeps it running smoothly. Regular maintenance stops unexpected breakdowns and saves you money.
Regular Inspection Schedule
- Do monthly checks on the whole system
- Look for wear or corrosion on electrical connections
- Check the evaporator and condenser coils for dirt or damage
- Test the temperature control every three months
Component Maintenance Guidelines
Each part of the system needs special care. Here are some key tips:
- Clean the evaporator coils after moving certain cargo
- Lubricate parts as the maker says
- Change filters when needed
- Check the refrigerant and pressure often
Documentation and Record Keeping
Maintenance Activity | Frequency | Responsible Personnel |
---|---|---|
Visual System Inspection | Monthly | Certified Technician |
Comprehensive System Check | Quarterly | Thermo King Dealer |
Detailed System Diagnostics | Annually | Authorized Service Center |
Professional tip: Keep detailed service logs. They track your unit’s health, predict problems, and support warranty claims. Keeping records is your best way to avoid system failures.
Safety Considerations When Addressing Code 26
When you’re fixing a Thermo King temperature control system, safety comes first. Dealing with Code 26 means you need to watch out for dangers that could harm the equipment and people.
Fixing a Thermo King unit needs careful safety steps. Here are some important safety tips for technicians and users:
- Always wear the right personal protective equipment (PPE)
- Turn off the electrical power before starting any checks
- Use insulated tools when working with electrical parts
- Check low-voltage circuits (24 Vac and 12 Vdc) before touching
- Look at safety decals on the Thermo King unit before starting work
Electrical safety is key when you’re figuring out Code 26. The control circuits have sensitive parts that need special care. I suggest getting help from a factory-trained Thermo King dealer who knows these systems well.
Handling refrigerants is risky. Only trained techs should handle it to avoid exposure or harm to the environment. Safe steps protect the tech and the refrigeration system.
Keep in mind, the Thermo King warranty is only good if authorized techs fix it. By focusing on safety and following the maker’s rules, you can fix Code 26 safely and avoid risks to people and equipment.
Conclusion
Dealing with Thermo King error codes can be tough. But knowing them is key to keeping your refrigeration unit running smoothly. I’ve learned that catching Code 26 early can save a lot of time and money.
To fix Thermo King Code 26, you need a clear plan. Regular checks, keeping records, and fixing problems fast are essential. This way, you avoid sudden breakdowns and keep your systems working great.
Think of your Thermo King unit as a big investment in your work’s efficiency. Knowing how to diagnose problems and working with experts keeps your equipment reliable and long-lasting. The secret is to always learn and keep up with maintenance.
By understanding and handling Thermo King error codes, you protect your cargo, cut down on downtime, and boost your business’s success. Stay informed, be ready, and your refrigeration units will be a valuable asset.