Choosing the wrong electrical wire can be a big problem. Many experts find it hard to pick between aluminum and copper wire. The wrong choice can cause safety issues, higher maintenance costs, and system failures.
I’ve looked into the main differences between aluminum and copper wire. These wires have special features that affect your project’s success. Knowing their properties helps you choose the right wire for your needs.

This guide will help you make the best wire choice for your electrical work. It’s useful for any project, big or small. You’ll learn how to pick the right wire for your electrical needs.
Understanding Metal Conductors in Electrical Wiring
Electrical conductors are key to our modern world. Choosing the right metal for wiring affects performance, safety, and efficiency. I’ve learned a lot about conductor selection in electrical systems.
Aluminum and copper have different electrical capacities. Let’s look at what makes each metal special for electrical use.
Basic Properties of Electrical Conductors
Metals vary in electrical conductivity. Copper is a standout with impressive stats:
- 100% IACS (International Annealed Copper Standard) conductivity rating
- Superior electrical transmission capabilities
- Lower resistance to electrical current flow
Aluminum has its own set of benefits:
- 61% of copper’s conductivity
- Significantly lighter weight
- 30% of copper’s total weight
Importance of Conductor Choice in Electrical Systems
Characteristic | Copper | Aluminum |
---|---|---|
Conductivity Ranking | 100% IACS | 61% IACS |
Weight per 1,000 ft | 65 lbs | 39 lbs |
Maximum Pulling Tension | 132 lbs | 157 lbs |
Market Trends in Wire Selection
Market trends show interesting changes in wire choices. Copper is the top pick for homes, but aluminum is growing in overhead lines. The debate between aluminum and copper is ongoing, with each metal excelling in different areas.
Aluminum vs Copper Wire: Core Differences
When we look at aluminum vs copper wire, we see big differences that affect how well electrical systems work. I’ve dug into the main traits that set these two common electrical conductor materials apart.
The biggest differences are in physical and electrical properties. Copper is about 60.78% better at conducting electricity than aluminum. This means copper wire is usually better at moving electricity in most cases.
- Copper has 40% better tensile strength compared to aluminum
- Aluminum wiring costs about 50% less than copper
- Aluminum requires 56% larger cross-sectional area to carry equivalent current
- Aluminum weighs roughly one-third of copper for similar resistance
When choosing between aluminum and copper wire, electrical engineers have to think about a few things. Aluminum is lighter, which is good for big projects. But copper is better at moving electricity, making it more reliable.
Aluminum conductors can carry about 40% less current than copper ones. This means they need careful planning in systems where moving lots of current is key.
Cost is also a big factor. Aluminum is much cheaper, which is great for projects where money is tight. This is true, even for big electrical jobs where costs can add up fast.
Copper Wire Properties and Applications
Copper wire is the most popular conductor in electrical systems. It’s used in commercial, industrial, and residential construction. Its exceptional characteristics make it a top choice for reliable and efficient electrical solutions.
Copper wire has remarkable electrical performance. It has high conductivity, allowing for smaller sizes while carrying more current. Compared to other materials, copper wire has impressive characteristics:
- 30% to 50% higher current carrying capacity
- More than 30% ductility
- Resistant mechanical wear capabilities
- Higher elasticity index
Conductivity and Performance
Copper wire excels in electrical applications. Its high conductivity means less energy loss and more reliable performance. It can handle high-stress electrical environments well.
Durability and Longevity
Copper wire’s durability is exceptional. It can withstand significant mechanical stress, outperforming other materials by about 40 percent. Its resistance to mechanical wear ensures long-term reliability.
Installation Requirements
Installing copper wire requires precision and understanding of its characteristics. Professionals must consider thermal expansion and connection techniques. Proper installation ensures optimal electrical conductivity and reduces maintenance issues.
Cost Considerations: Price Per Pound Analysis
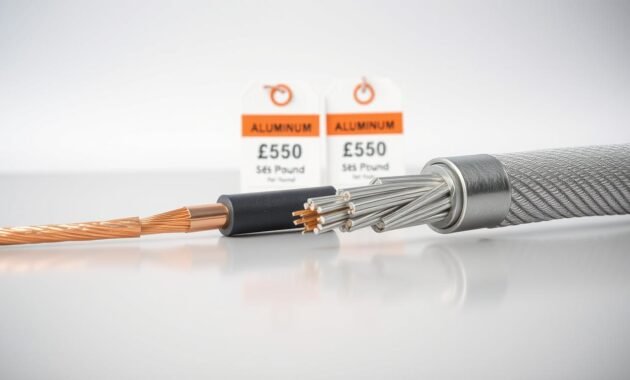
When choosing electrical wiring for a commercial building, aluminum needs careful cost analysis. The cost of wire can greatly affect project budgets and future expenses.
Let’s look at the key pricing factors:
- Copper wire currently ranges from $3.35 to $3.60 per pound
- Aluminum wire sits at approximately $2,028 per ton
- Primary aluminum costs around $2,700 per metric ton
For commercial building projects, aluminum is a cost-effective choice. Its lower price compared to copper makes it appealing for projects watching their budgets. In big installations, the cost savings can be significant.
Important price factors include:
- Material cost per pound/ton
- Quantity needed for the project
- Long-term performance expectations
- Installation complexity
Market trends show aluminum prices will likely stay between $2,700 and $2,813 per ton by 2025. This makes aluminum a more affordable option for electrical systems. While copper is the top choice, aluminum is a budget-friendly alternative for many commercial electrical needs.
Safety Aspects of Different Wire Types
Electrical wiring safety is all about knowing the materials and risks. When using metals like aluminum and copper, it’s key to understand their differences. This helps avoid electrical dangers.
How wires are pulled and connected is vital for safety. Each metal has its own risks and benefits. These affect how well and safely the wiring works over time.
Fire Risk Assessment
Aluminum wiring has its own set of safety issues compared to copper. Here are some important facts about fire risks:
- Aluminum wiring can lead to more fires because of its expansion and contraction
- Loose connections can greatly increase the risk of electrical fires
- It’s very important to install aluminum wiring correctly to avoid safety risks
Connection Stability
How well wires connect is a big deal for safety. Copper is better in this area for several reasons:
Wire Material | Connection Stability | Fire Risk |
---|---|---|
Copper | High stability | Low risk |
Aluminum | Lower stability | Higher risk |
Long-term Safety Considerations
Choosing the right wire means looking at long-term performance and wear. Copper lasts longer with less upkeep. Aluminum needs regular checks to stay safe.
- Copper has fewer expansion cycles
- Aluminum needs special compounds at connections
- Checking connections often is key for aluminum wiring
Knowing these safety details helps both pros and homeowners pick the best wire and install it right.
Installation Challenges and Solutions
Installing electrical wiring can be tricky, even more so with aluminum conductors. I’ll explain the main challenges and offer practical solutions. This will help you tackle these issues with confidence.
Read also: Electrical Weatherhead Installation
Aluminum conductors need special care during installation. They are bigger than copper wire, so you must plan for their size. This size difference affects several important parts of electrical wiring:
- Increased raceway requirements
- Specialized connection techniques
- Unique preparation methods
Installing aluminum conductors requires great precision. These wires need about 50% more space than copper wires. You’ll likely need to make conduit sizes 5-7 percent bigger.
Installation Challenge | Solution |
---|---|
Oxidation Issues | Apply antioxidant joint compound |
Limited Flexibility | Use specialized stripping tools |
Larger Wire Size | Select two wire gauge sizes larger than copper |
Experts suggest quality control steps. These include checking at energization and follow-up checks 30-60 days later. These steps ensure your aluminum electrical system works well for a long time.
Aluminum conductors may pose challenges, but knowing these can help you succeed. With the right preparation and technique, you can overcome aluminum wiring’s unique traits.
Read also: What Size Generator Do I need for My House ?
Commercial Building Applications
Choosing the right wire is key for commercial building electrical systems. The wiring’s electrical capacity and performance affect the building’s function and safety.
Electrical engineers must decide between aluminum and copper wiring for big projects. My research shows important factors that affect wire choice in commercial buildings.
Large-Scale Project Requirements
Commercial buildings need strong electrical systems. Important factors in picking wire include:
- Total electrical load capacity
- Installation complexity
- Long-term maintenance costs
- Building code compliance
Load Capacity Considerations
Wire Type | Conductivity | Current Carrying Capacity | Cost Efficiency |
---|---|---|---|
Aluminum | 60% | Requires 67% more thickness | 50% cheaper |
Copper | 100% | Higher current capacity | More expensive |
Cost-Efficiency Factors
Aluminum wiring is cheaper for commercial projects. It can save thousands of dollars. New methods have fixed old problems, making aluminum a good choice.
It’s wise to look at each project’s electrical needs and budget. Check local codes and talk to electrical experts for the best wire choice.
Maintenance and Long-Term Performance
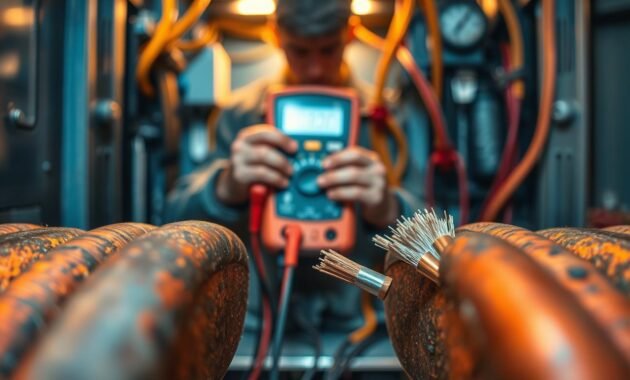
Maintenance is key for electrical wiring to last long and stay safe. Aluminum wiring needs extra care compared to copper. This makes keeping electrical systems in good shape very important.
My research shows several important maintenance factors for different wire types:
- Copper wiring is very durable and needs little maintenance
- Aluminum wiring needs more checks because of oxidation risks
- Dissimilar metals can cause connection problems that need a pro’s look
Keeping aluminum wire in good shape is a challenge. Its high thermal expansion rate can loosen connections over time. This can be dangerous. Homeowners should get professional checks every 3-5 years to spot any problems.
Important maintenance steps for aluminum wiring include:
- Using special anti-oxidation compounds at terminal points
- Looking for signs of overheating at connection points
- Watching electrical resistance and connection stability
The performance of electrical wiring over time depends a lot on maintenance. While aluminum wiring might be cheaper, it needs more care to be safe and reliable. This is compared to traditional copper wire systems.
Future Trends in Electrical Wiring
The world of electrical wires is changing fast. New technologies are making big changes in how we wire things. These changes are all about making things better and greener.
There are exciting trends coming up in electrical wiring:
- Smart materials with better conductivity
- More focus on saving energy
- Greener ways to make wires
- New insulation technologies
More people want electric cars, which is driving new wire tech. Copper is the top choice for building wires, used in 93% of them. It’s great because it conducts electricity well and doesn’t rust easily.
New wire designs are tackling big problems:
- Creating smaller wire setups
- Materials that conduct better
- Lower costs for setting up and fixing
- Better handling of heat
The future of electrical wires will focus on being better, safer, and kinder to the planet. New tech will bring us more efficient, dependable, and flexible wiring for today’s needs.
Conclusion
Exploring aluminum vs copper wire shows it’s not just a simple choice. Each wire has its own strengths for electrical systems. Copper wire is top-notch for carrying electricity, with about 40% better flow than aluminum.
Aluminum wire is great for saving money, being 50% lighter and cheaper than copper. It’s perfect for big projects and power lines. Knowing what you need is key, whether it’s handling current, saving on costs, or lasting long.
Choosing the right wire depends on your project’s needs. Copper is best for high-stakes areas like aerospace and solar. Aluminum is better for utility lines and overhead work. Keeping up with wire technology helps everyone make better choices.
There’s no one-size-fits-all in electrical wiring. Your project’s budget, needs, and setting will decide between aluminum or copper. It’s all about what works best for you.